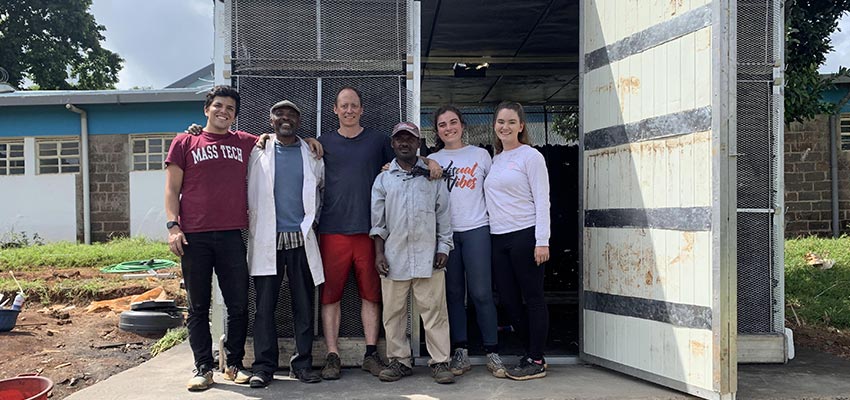
Since the time of the work described in the blog post below, Kenya has confirmed 384 cases of Covid-19 and the University of Nairobi campus has closed. A report by global think tank Overseas Development Institute titled Economic Vulnerabilities to Health Pandemics has identified Kenya as one of the countries most likely to suffer huge economic impacts due to the virus (article). The pandemic, along with recent waves of locusts in East Africa are both affecting the food supply. The need for lowcost and effective means for preserving vegetables and increasing access to nutritious food may never have been greater.
In January, during MIT’s Independent Activities Period (IAP), I traveled to Nairobi, Kenya with my UROP supervisor, MIT D-Lab Research Engineer Eric Verploegen, to extend our research on evaporative cooling technology. Also traveling and working with us were Alex Encinas and Maddy Bundy, both students from D-Lab’s class Applications of Energy in Global Development. With this project, we are exploring new evaporative cooler designs that use more sustainable materials, while improving performance and usability.
First, we built a room-sized evaporative cooling chamber on campus at the University of Nairobi to have an easily accessible, controlled research setting to collect data from and evaluate various designs. The chamber that we constructed is modular, which allows for modifications to be easily made and gives us the ability to test various configurations and determine the relative effects of various features.
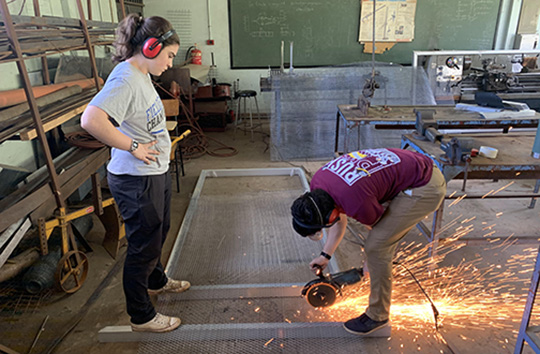
Our work over the three weeks that we were in Kenya required us to source the materials, finalize our design, then construct the chamber. After arriving in Nairobi, our first task was to meet with our collaborators at the University of Nairobi, Professors Jane Ambuko, Duncan Mbgue, and Mwachoni El-Yakhim as well as postgrad student Benson Maina. Mr. Mwachoni worked with us intensely on the design of the chamber and gave us free rein of his workshop to build our chamber. He took us to visit local markets to find readily available materials and connected us to local contractors to help construct elements of our design such as the ceiling and fiberglass tanks for the water collection and recycling system.
Luckily, for constructing the chamber, we had extra help from Boniface Manambo, who had done parts of the construction for all the chambers we are currently studying. We faced a challenge in the form of unruly expanded mesh that took a few days to fit into our frames and gave us immediate insight into the necessity of finding easier materials to use. After finishing the framing of the walls, we brought them to the site to start erecting the chamber. The next challenge we encountered was putting the charcoal into the walls. Pouring the charcoal produced so much dust, took so much time, and made it very difficult to fill all the space. I was grateful to be able to try this out to see just how difficult this process is and how helpful a new material would be.

We decided to make the wall panels removable to allow for a quick exchange of materials. Another design element we wanted to investigate was airflow within the chamber. We mounted a fan in the ceiling to suck air out of the chamber and pull air through the evaporative cooling media faster. In order to monitor the effectiveness of the fan from back home, we placed Sensen sensors throughout the test chamber to record temperature, moisture, and humidity readings from various locations. These data-logging sensors are specifically designed for evaporative coolers and record data in five-minute increments from spots all over the chamber.
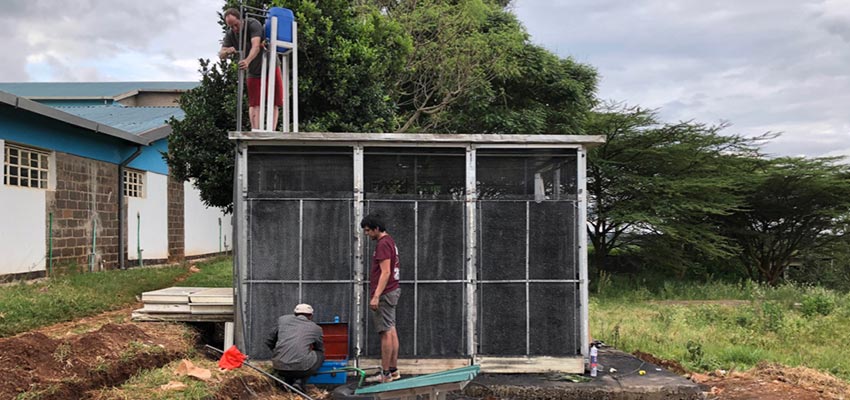
We also had the opportunity to visit rural farming cooperatives in Karurumo and Masii to check in on the charcoal coolers there and hold focus groups with some cooperative members. We discussed how the cooperative uses their cooler, what works well, what challenges they have, what improvements they would like to see, and we heard their thoughts on potential design changes that we suggested. Both cooperatives primarily use the evaporative coolers to extend the storage life of their mangoes so that they can be processed into other goods such as juice and fruit leather. The room-sized coolers also allow for the centralization of their harvests, which results in consistent, higher prices from buyers. However, they expressed concern about the use of charcoal as it tends to be expensive and charcoal production is bad for the environment. The farmers also hoped to find a way to recycle the water used in the system as they have to pay for the water used to cool the chamber. Our experimental chamber is testing materials that may be able to replace charcoal a recycling system that uses two holding tanks, fiberglass water catchers, and a pump to recirculate the water.
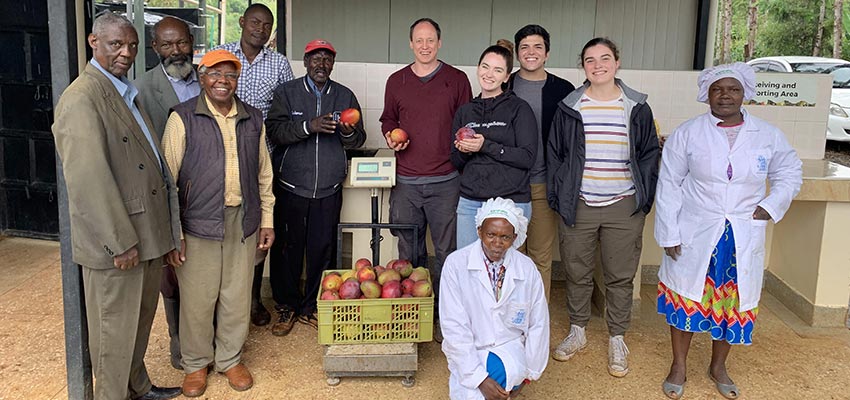
I enjoyed going on this trip because it gave me the context for the research I have been working on all year. During the fall semester, I worked on modeling the evaporative cooling process in Matlab using a simulation of the thermodynamic and transport processes involved. I also helped to develop the data analysis code to help us process the data from the Sensen boxes. Since most of my UROP work has been virtual, I reveled in the opportunity to participate in a hands-on aspect of the project. Participating in the focus groups also gave me the perspective of the people that this research directly impacts and gave insight into how the research can expand to help as many people as possible. Finally, actually constructing a chamber of our own gave me first-hand experience of the motivation behind the design changes we are looking to make. I am looking forward to continuing to contribute to our research on evaporative cooling and innovate to discover new designs.
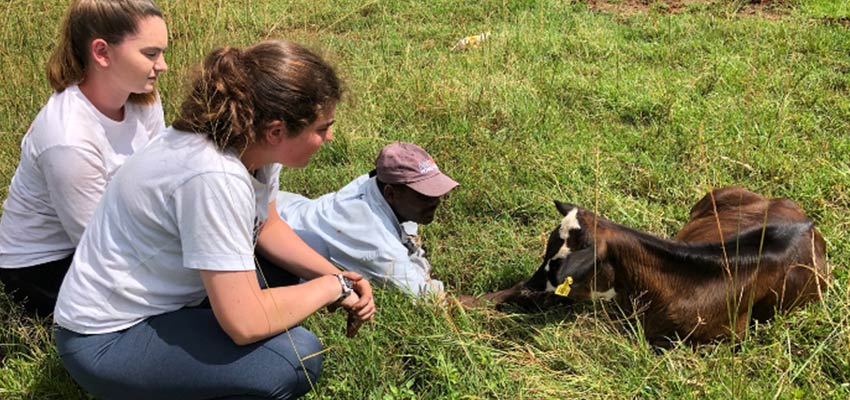
This work was funded in part by a seed grant from the Abdul Latif Jameel Water & Food Systems Lab (J-WAFS).
About the author
Christine Padalino is a sophomore at MIT majoring in Chemical Engineering and Earth, Atmospheric, and Planetary Sciences. She is interested in developing alternative energy solutions and climate change mitigation. Through her UROP with D-Lab, she has been able to explore these interests through the lens of global development.
More information
MIT D-Lab Evaporative Cooling for Vegetable Preservation
Contact
Eric Verploegen, MIT D-Lab Research Engineer, Evaporative Cooling Lead